
Data Structure
Networking
RDBMS
Operating System
Java
MS Excel
iOS
HTML
CSS
Android
Python
C Programming
C++
C#
MongoDB
MySQL
Javascript
PHP
- Selected Reading
- UPSC IAS Exams Notes
- Developer's Best Practices
- Questions and Answers
- Effective Resume Writing
- HR Interview Questions
- Computer Glossary
- Who is Who
Needs and Strategies for the Six Sigma Control Plan
Six Sigma methodologies are well?known for their data?driven, logical approach to problem?solving. What truly separates them from other quality theories is their adaptation and usefulness outside manufacturing, where they were born.
One of the key objectives of Lean Six Sigma is to reduce unnecessary phases and waste in a process or business model. The lean approach eliminates any process that offers no value to enhance efficiency, workflow, and profitability.
Organizations create Control Plans to help management monitor measurements, document accomplishments, and make changes for continuous process improvement. A Control Plan is a method of documenting the functional parts of quality control that will be carried out. This will guarantee that the quality criteria for a given product or service are met.
This Control Plan might be created for a process, a phase of the process, a piece of equipment, or something else entirely. Here's a quick rundown of the needs and strategies for a Six Sigma Control Plan.
What is a Six Sigma Control Plan?
A Control Plan is a written overview of the process that defines the measures to be performed. This is to keep an operation or a device functioning at its present level of performance. Control Plans describe each stage of the process and the metrics that must be monitored. This will guarantee no excessive deviations from mean performance or variance in a batch of goods.
Control Plans are widely used by Six Sigma experts and are an essential component of the Six Sigma methodology set.
What Does a Six Sigma Control Plan Do?
According to the American Society for Quality (ASQ), the Control Plan's goal is to guarantee that performance gains produced by the project team are sustained throughout time.
The plan is developed during the improvement phase of the define, measure, analyze, improve, control (DMAIC) methodology or an equivalent step of other methods.
A Control Plan, in essence, offers a summary of all the information pertinent to a specific project. This is so that the quality specialist can determine if the project is on track and, in the event of deviations, delays, or excessive overheads, may take remedial action. As a result, the Control Plan is kept up to date to reflect any changes to the process, which may include (but is not limited to)?
An adjustment or alteration to a process step
Addition or deletion of a process step
Human resources and training need to change
Equipment used in the process may be added or removed
Capital and financial inflows and outflows have changed
The Control Plan template is created at the start of a project. It is developed with or without the input of all stakeholders engaged in a specific project, beginning with the process or product owner.
What is Included in a Standard Control Plan?
Control Plans may have as many or as few components as necessary to cover the breadth of the process or project under consideration. A typical Control Plan includes the following items?
Process Flowchart ? A visual depiction of the process workflow with decision?making phases highlighted is included in many Control Plans. This is a high?level summary of the process that may be referred to at any point and by any stakeholder.
The CTQs are the major quantitative and measurable features of a product or process that must meet performance standards or specification limitations to satisfy the client. This aids in the alignment of design parameters with customer needs.
Process Phase ? This column contains the name or title of the process step. For example, in a backyard garage, a polishing operation utilizing lathes may include tool preparation, rough polishing, fine polishing, and delivery as the many processes involved in the overall process.
Specification Characteristic ? To quantify a CTQ, a specific product characteristic must be selected for measurement? this column is used to record the specification's attributes. For example, the diameter of the shaft to be polished.
Specifications? Use this item to enter the numerical values of the specifications and the unit of measurement. E.g., 4mm internal diameter; 7.5mm exterior diameter.
Measurement Technique ? Use this column to describe the method used to specify the measurement. E.g., Calipers Vernier.
Size of the sample ? The size of the sample used for measurement.
Measurement Frequency ? Indicates how often samples are selected for measurement on an hourly, daily, and so on basis.
Corrective Action ? Any corrective measures implemented at that specific phase in the process are documented and recorded for future use.
Standards ? The quality standards applied and the SOP (Standard Operating Procedure) guidelines may be noted for enterprises' manufacturing operations and Control Plans.
Additional documentation may include information such as the person taking the measurement, the date, place, and time the recording was created, the revision number and version control, the location, and so on.
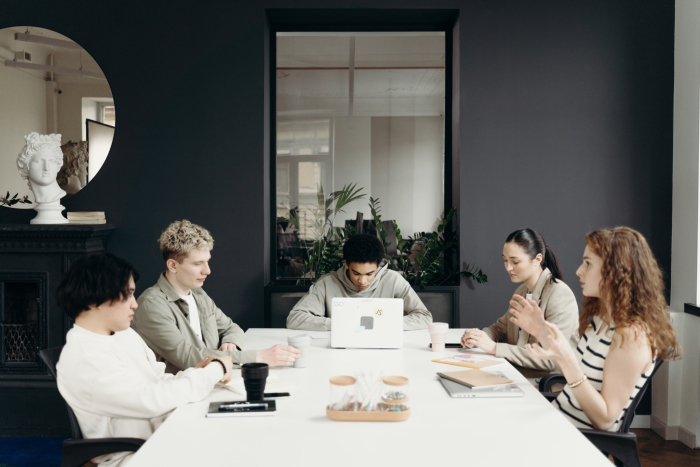
What You Should Know Before Creating a Control Plan?
Six Sigma Lean Control Plans are critical decision?making tools and should be developed after a thorough evaluation and assessment of the project's product status from all perspectives. Before the project can begin, several factors must be considered.
Input and Output ? The different IO parameters and the stages at which they enter the exit Control Process must be determined. This will guarantee that control information flows freely, which is critical to the project's success.
Specifications and Metrics ? A Control Plan should be created after thoroughly examining client perceptions and expectations. This guarantees that the finished product/service meets the standards of the client.
Frequency of Reporting and Sampling ? A predetermined timetable enables ample time to address any problems. Regular audits provide tighter control and monitoring.
Process Design and Implementation ? The Control Plan is based on the central process. It is developed through the establishment of proper standards and performance criteria.
Corrective Actions ? A framework for implementing disciplinary actions should be included in every Control Plan.
Process Owner Identification and Documentation ? Process owners are individuals or groups of individuals accountable for and have the power to make changes to the process as the project progresses. Identifying process owners early on is critical to establishing accountability.
Recording ? Information must be documented at all project phases to aid planning, testing, execution, and evaluation. Plan sheets capture and maintain information about a product or process.
What Are the Benefits of Using a Control Plan?
A Control Plan is a one?stop shop for learning about the process's features, requirements, and standard operating procedures (SOP). A CP provides for the assignment of responsibility and the distribution of liability for each activity in the process.
This ensures that the process works smoothly and is long?term viable. A well?designed Control Plan assists process and product owners in tracking and correcting KPIV and KPOV performance and minimizing negative business consequences from faults and process degradation (Key Performance Input and Output Variables).
Conclusion
Control is one of the final phases of the Define?Measure?Analyze?Improve?Control Lean Six Sigma process improvement roadmap (DMAIC). Creating a well?thought?out Control Plan to limit the risk of adverse business repercussions due to process degradation is one of the most significant parts of the 'Control' stage.
A Control Plan frequently includes procedures that must be executed on time, especially when performance measurements go outside of a pre?defined, planned range. Furthermore, an organizational framework must be in place to hold all process owners accountable for implementing the different portions of the Control Plan. This is especially true for those related to their areas of operations.
The process owner and his assigned team must develop this Control Plan to increase service quality. This plan should be malleable enough to be updated in response to post?implementation assessments and modifications.