
Data Structure
Networking
RDBMS
Operating System
Java
MS Excel
iOS
HTML
CSS
Android
Python
C Programming
C++
C#
MongoDB
MySQL
Javascript
PHP
- Selected Reading
- UPSC IAS Exams Notes
- Developer's Best Practices
- Questions and Answers
- Effective Resume Writing
- HR Interview Questions
- Computer Glossary
- Who is Who
Spend Analysis, Six Sigma, and Business
Introduction
Business success in the modern cutthroat marketplace depends on efficient cost management. The key to effective cost oversight is comprehending and analyzing expenditure statistics. The bottom line may be greatly improved and productivity in operation can be significantly enhanced by using Six Sigma approaches. This article investigates how expenditure analysis, Six Sigma, and their effects on business achievement relate to one another.
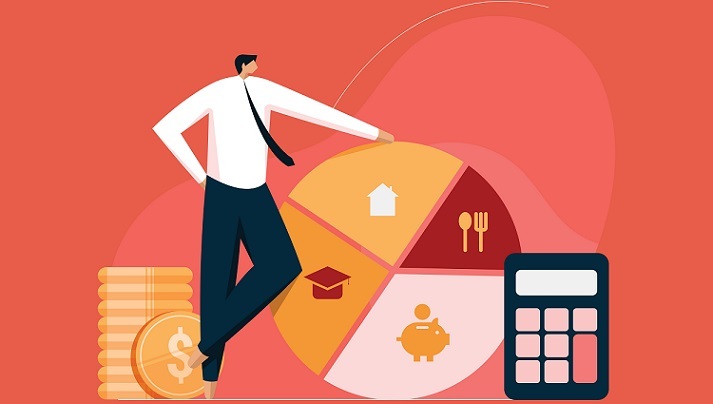
Importance of Spend Analysis
A crucial part of Six Sigma methodology, efficient spend analysis offers businesses insightful information about their sourcing and buying procedures. In order to improve business efficiency and client fulfillment, Six Sigma attempts to eradicate faults and minimize variability in processes.
Spend analysis may help organizations find cost-cutting possibilities, improve relations with vendors, and influence strategic choice making by integrating into the Six Sigma methodology. This essay examines the value of expenditure analysis in Six Sigma, showing its advantages and how it helps projects to enhance processes succeed in general.
Cost Reduction Opportunities ? Spend analysis is essential in locating cost reduction possibilities in a company's buying processes. Organizations can spot inefficiencies, wasted expenditures, and failure to comply with regulations by carefully examining expenditure habits and vendor performance.
Making Decisions Based on Data ? Spend analysis offers the crucial information needed for educated decisions, which is the foundation of Six Sigma. Spend data may be gathered, arranged, and analyzed to provide organizations with a thorough insight into their buying operations
Assessment and Optimization of Supplier Productivity ? Spend analysis enables businesses to assess the performance of their suppliers and make well-informed choices about how they work together. Organizations may identify failing vendors, analyze delivery times, gauge productivity, and verify adherence to contracts by analyzing expenditure data.
Risk Reduction and Conformity ? Within Six Sigma efforts, spend analysis helps with risk reduction and management of compliance. Organizations can discover possible hazards including violation of contracts, a single provider dependency, and conformity with purchasing laws by analyzing expenditure data.
Continuous Improvement ? Spend analysis helps Six Sigma efforts develop an environment of continual enhancement. Organizations can assess the success of cost-cutting efforts, spot opportunities for enhancement, and follow the results of adopted policies by routinely analyzing expenditure data.
Organizations may use this data-driven strategy for making choices that are based on actual purchasing patterns, vendor performance measures, and past trends. Spend analysis may be included in the Six Sigma architecture to help organizations make certain that process enhancement efforts are founded on reliable data, producing outcomes that are more significant and successful.
Organizations can continuously handle these risks thanks to this research, which also helps them put risk-reduction plans in place and guarantee conformity to regulations. Spend analysis may be included in Six Sigma to help businesses avoid expensive interruptions and keep their purchasing practices strong and legal.
Overview of Six Sigma
In order to reduce process variances, flaws, and mistakes inside organizations, Six Sigma is rigorous and informed by data technique. It concentrates on reaching almost flawless levels of operational effectiveness and ongoing advancement in both qualities. Six Sigma's core values consist of ?
Data-Driven Approach ? Six Sigma combines statistical assessment and data-driven decisions to pinpoint the sources of issues, gauge process effectiveness, and spearhead initiatives to improve
DMAIC Methodology ? DMAIC is a systematic system for handling challenges that is used in Six Sigma initiatives. It stands for "Define, Measure, Analyze, Improve, Control." It offers an easy-to-follow process for improving operations, from difficulty description through long-term management of the methods that have been modified.
Process Improvement Tools ? Six Sigma uses a variety of techniques and instruments for the improvement of processes, including map-based statistical analysis, root-cause investigation, and testing hypothesis.
Concentration on client Contentment ? Six Sigma places a strong emphasis on comprehending and fulfilling client requirements while guaranteeing those procedures produce products and solutions with the fewest possible flaws and deviations.
Integration of Spend Analysis and Six Sigma
Businesses may gain a lot from the combination of expenditure analysis and Six Sigma. Organizations may develop cost control plans that are more extensive and effective by integrating these techniques. The integration may be accomplished as follows ?
Possibilities for Cost Reduction ? Spend analysis reveals trends in expenditure and points out places where Six Sigma approaches may be used to save expenses. Six Sigma methods, for instance, may be used to simplify procedures, boost effectiveness, and get rid of waste by recognizing typical causes of faults or bottlenecks in the buying process.
Supplier Performance and Quality Improvement ? Spend analysis gives businesses the ability to evaluate supplier efficiency, covering timely delivery and excellent data. Six Sigma approaches may be used to locate vendors with recurring quality problems, address their underlying causes, and enhance supplier performance.
Process Optimization and Waste Reduction ? Spend analysis and Six Sigma may help firms find inefficiencies in processes and wasteful areas, which leads to procedure optimization and decreases waste. Businesses can identify delays in processes, duplications, and superfluous procedures by analyzing expenditure data. Then, processes may be streamlined and waste can be eliminated using Six Sigma methods like value stream visualization or procedure capability analysis, which will increase productivity and save costs.
Regulatory and Risk Prevention ? Spend analysis provides light on risks and regulations relating to suppliers. Organizations may identify risks' underlying causes, create methods for mitigating them, and build strong controls to assure conformity by incorporating Six Sigma processes.
Business Impact and Case Studies
Substantial effects on business profitability have been seen as a result of the combination of expenditure analysis with Six Sigma. Numerous case studies point forth the advantages ?
Cost-Savings Possibilities ? A global production company used Six Sigma methodologies to analyze expenditure data and find cost-saving possibilities. The business obtained 14% yearly reductions by simplifying buying processes, improving agreements with vendors, and cutting back on non-value-added operations.
Quality Improvement ? To solve reliability challenges in its supply chain, a vendor to the automobile industry combined expenditure analysis with Six Sigma. The organization decreased faults by 35% and raised consumer happiness through the analysis of expenditure data and partnership with providers to enhance quality control procedures
Risk Reduction ? A healthcare organization used expenditure monitoring and Six Sigma to pinpoint risks associated with suppliers and guarantee that all legal criteria were being met
Process Improvement ? To speed up the processing of invoices and payments, a financial service organization used Six Sigma and expenditure monitoring. The organization cut the turnaround time by 35% by analyzing expenditure data and automating the billing process, which boosted cash flow and strengthened connections with suppliers.
Conclusion
When correctly combined, the approaches of expenditure analysis and Six Sigma may produce notable gains in cost control, operational effectiveness, and business results. Spend analysis delivers information on expenditure patterns and supplier effectiveness, while Six Sigma provides strategies and instruments for streamlining processes and cutting waste.
Organizations may find cost-saving possibilities, enhance quality, streamline operations, reduce risks, and guarantee conformance by integrating these techniques.
Organizations may implement sustained budgeting methods, improve client retention, and gain an unfair advantage in the marketplace by integrating spend analysis with Six Sigma. In today's changing business climate, organizations that adopt these approaches and promote an atmosphere of decision-making based on data and perpetual enhancement may achieve for a long time profitability as well as success.