
Data Structure
Networking
RDBMS
Operating System
Java
MS Excel
iOS
HTML
CSS
Android
Python
C Programming
C++
C#
MongoDB
MySQL
Javascript
PHP
- Selected Reading
- UPSC IAS Exams Notes
- Developer's Best Practices
- Questions and Answers
- Effective Resume Writing
- HR Interview Questions
- Computer Glossary
- Who is Who
Six Sigma for Service Industries: A Guide
Introduction
The phrase "Six Sigma for Service Industries" describes the use of the Six Sigma approach, which was first created for the manufacturing industry, to boost productivity as well as quality in service-oriented industries. Utilizing information-driven decisions and methodical problem-solving methodologies, Six Sigma targets lowering defects, decreasing process variation, and improving client retention.
Despite the fact that the service sector differs from the manufacturing sector in terms of qualitative outcomes and client contacts, Six Sigma techniques may be adequately adopted and utilized to address problems and promote enhancements to processes in the service sector.
Service organizations may increase productivity, cut down on mistakes, as well as improve client experiences by implementing the DMAIC (Define, Measure, Analyze, increase, Control) approach and a number of tools and techniques.
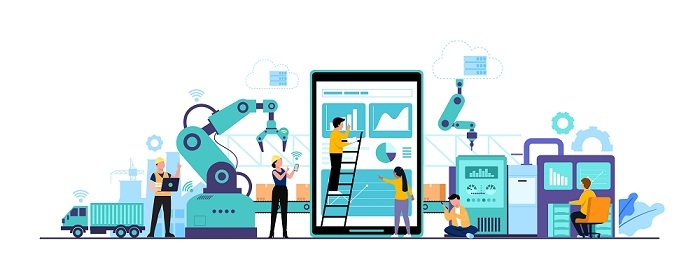
Six Sigma, which was first created for manufacturing processes, is today a commonly used approach for enhancing quality and productivity in service-related businesses. It has been demonstrated that applying Six Sigma ideas and techniques to supply chain operations is a very successful way to find and eliminate flaws, reduce variability, improve customer happiness, and promote performance excellence.
By emphasizing its core ideas, methodology, and advantages, this manual attempts to give a general introduction of Six Sigma in the surroundings of the service sectors.
Understanding Six Sigma in Service Industries
The Six Sigma approach was initially created for the manufacturing sector and has now been modified for the service sector.
It concentrates on raising client fulfillment while lowering faults and raising quality.
In contrast to manufacturing, service sectors differ in that they focus more on qualitative products and client relationships.
To find and get rid of mistakes and variances, customer service procedures might use Six Sigma concepts.
In Six Sigma for business services, the DMAIC (Define, Measure, Analyze, Improve, Control) technique is frequently employed.
Voice of the Customer (VoC) analysis, method mapping, statistical examination, and lean concepts are important tools and methodologies.
Increasing productivity, enhancing customer happiness, and making data-driven decisions are all advantages of applying Six Sigma to support businesses.
Due to the tangible character of offerings, reluctance to change, and complexity of service procedures, difficulties may occur.
Numerous service industries, including healthcare, hotels, finance, and internet access, have excellent stories to share.
For service organizations looking to achieve extraordinary service delivery and consumer experiences, the Six Sigma approach is still useful.
DMAIC Methodology for Service Improvement
An efficient framework for enhancing services in business sectors is the DMAIC technique, which is frequently employed in Six Sigma. Here is a quick summary of each stage:
Define
Specify the aims and purposes of the project.
Recognise the demands and expectations of the consumer.
Identify the procedure for providing service that needs to be enhanced.
Create measurements for performance metrics.
Measure
Gather pertinent information on the present service procedure.
Establish measurements and key performance indicators (KPIs).
Evaluate the previous year's performance by analyzing the data.
Determine any discrepancies between current results and intended objectives.
Analyze
Examine the customer service process in great detail.
Determine the underlying reasons for any flaws, mistakes, or deviations.
Employ tools like Pareto graphs, procedure maps, and cause-and-effect diagrams.
Set priorities for the urgent problems that must be solved.
Improve
Come up with potential answers to the problems you've discovered.
Execute enhancements to the process and, if required, restructure.
Utilize methods such as process optimisation, robotics, and error-proofing.
On a modest basis, pilot and evaluate the suggested improvements.
Control
Create control systems to keep the advancements going.
Create mechanisms for tracking and surveillance.
Put standard operating procedures (SOPs) into action.
Utilize quantitative control diagrams to consistently track and evaluate performance.
Key Tools and Techniques in Six Sigma for Services
Numerous tools and approaches are used in Six Sigma for services to analyze data, find the underlying causes, and promote process changes. Here are some essential methods and tools:
Evaluation of the voice of the customer (VoC)
For a deeper comprehension of the needs and requirements of your customers, collect comments and observations.
Utilize methods like interviews, polls, and focus groups to get client viewpoints.
Convert client needs into quantifiable measures and adjust service operations as necessary.
Method Mapping
Visualize and record processes for service to comprehend their relationships, movement, and stages.
Determine waste, bottlenecks, and areas for enhancement.
To analyze and simplify processes, use tools like schematics, swim lane diagrams, and worth stream maps.
FMEA stands for Failure Mode and Effect Analysis:
Determine the weak places in the service procedures.
Determine how failures may affect customer service and satisfaction.
Create preventative actions to lessen hazards and increase the dependability of the process.
Analytical Statistics:
Use statistical techniques and applications to analyze data and come to intelligent judgments.
To verify hypotheses and reach data-driven judgments, use hypothesis validation.
Use a regression approach to find the connections between the parameters.
Monitoring graphs may be used to track process efficiency and spot changes.
Benefits and Challenges of Implementing Six Sigma in Service Industries
Benefits
Improved levels of client happiness are the outcome of Six Sigma's emphasis on satisfying client criteria and minimizing defects, which leads to better interactions with clients.
Reduction in mistakes and flaws: Six Sigma assists in reducing errors, imperfections, and service breakdowns by locating and treating their root causes.
Enhanced efficiency and effectiveness in operations are brought about by the Six Sigma methodology simplification of delivery procedures and elimination of waste.
Improved operational visibility: Six Sigma technologies offer new perspectives on service processes, enabling organizations to see obstacles, waste, and possibilities for change.
Making decisions based on data: Six Sigma places a strong emphasis on the application of research methods and information analysis, allowing businesses to arrive at decisions that are well-informed and supported by solid facts.
Challenges
The intangibility character of offerings makes it difficult to gauge and enhance process efficiency since they frequently entail immaterial customer interactions and outputs.
Employees acclimated to current procedures may be resistant to the changes that Six Sigma implementation calls for in procedures, duties, and attitudes.
Data Accessibility and Quantity: It can be difficult to access precise and reliable information in the service sectors, necessitating the development of dependable data collecting and evaluation techniques.
Service processes are complicated because they frequently contain several interaction points, connections, and variances, making it difficult to pinpoint and correct the primary sources of errors.
Organizational Environment: Establishing a Six Sigma culture calls for solid dedication from the top, active employee participation, and alignment with organizational objectives.
Conclusion
Finally, Six Sigma has transformed from a manufacturing-centric technique to a potent framework for enhancing the level of service and operational effectiveness in companies providing services. Service organizations may increase customer happiness, get rid of errors, cut down on variability in processes and make long-lasting changes by using the DMAIC approach and a variety of techniques and instruments.
Effective instances show the benefits of applying Six Sigma in industries including medical care, hotels, finance, and telecom despite difficulties connected to the ephemeral structure of services and reluctance to make changes.
Six Sigma remains to be an invaluable resource for service organizations aiming to provide outstanding experiences for customers while attaining operational success because of its consumer-centric emphasis and decision-making based on information.