
Data Structure
Networking
RDBMS
Operating System
Java
MS Excel
iOS
HTML
CSS
Android
Python
C Programming
C++
C#
MongoDB
MySQL
Javascript
PHP
- Selected Reading
- UPSC IAS Exams Notes
- Developer's Best Practices
- Questions and Answers
- Effective Resume Writing
- HR Interview Questions
- Computer Glossary
- Who is Who
The PDSA Technique for Quality Improvements
The PDSA technique is a proven method for improving the quality of any process. It stands for Plan-Do-Study-Act, and it encourages organizations to break down their processes into smaller chunks to improve overall quality. PDSA is one of the important processes for a business to operate efficiently. In this article, we shall discuss the advantages of the PDSA technique, how to apply it to your organization, and how it can help you achieve better-quality results.
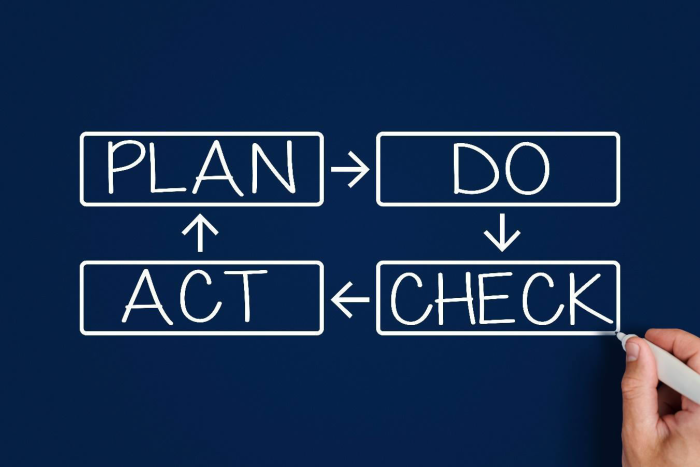
What Is The PDSA Technique?
The PDSA technique (Plan-Do-Study-Act) is a quality improvement method developed by two renowned American statisticians, Walter A. Shewhart and W. Edwards Deming. It was designed to help organizations improve their operations through the use of statistical methods. The PDSA cycle is based on four main steps: plan, do, study, and act.
The "plan" phase of this technique involves determining the problem or issue to be olved. This step includes setting objectives and gathering data related to the issue. The "do" phase revolves around putting the plan into action. During this phase, the organization should identify ways to address the issue and other potential barriers, if any. The "study" phase measures the results of the activities that were implemented during the "do" phase. This includes collecting data to measure success and identifying any areas that need improvement. Finally, the "act" phase involves making changes based on the data collected during the study phase. These changes can include changes to processes, systems, or people.
The PDSA technique is a great tool for organizations to improve their operations and achieve their goals. It can help identify the root causes of issues and provide an efficient way to measure success. Additionally, it encourages an iterative process that can help organizations quickly identify and solve problems.
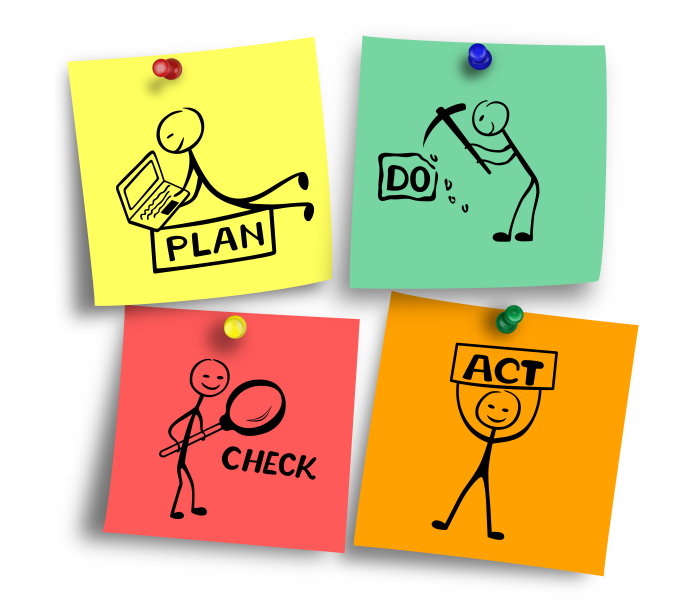
How Does The PDSA Technique Work?
At its core, the PDSA cycle is designed to measure and improve an existing process or system. It involves four distinct steps: plan, do, study, and act. The PDSA technique is a powerful tool for quality improvement teams because it helps them focus their efforts on making small, incremental changes that can have a big impact on their organization's performance. Here is how the PDSA technique works ?
Plan Phase
During the planning stage, the team identifies an area where they think improvements can be made and creates an action plan to make those improvements. This involves clearly defining the problem to be addressed and outlining the steps needed to address it. During the planning stage, it is important to identify potential risks and develop a plan for addressing them. With the objectives of the PDSA technique in place, you need to identify the relevant folks who will be in charge of making the changes in product quality. Finally, a detailed plan to improve the current production process is necessary for the PDSA team to succeed.
Do Phase
Once the plan is complete, it's time to execute it. The goal here is to collect data that will help you assess the effectiveness of your efforts. This includes carrying out the planned changes and measuring the results of these changes. The manager must communicate the PDSA plan to the team and keep their morale high while executing such changes. The execution of quality improvement plans must be time-bound and should deliver measurable results. The PDSA team must evaluate the new process at regular intervals to see if the obtained results are as per the expectations of their original plan. In case of any deviation, the manager must identify control measures to fix the bottlenecks.
Study Phase
After the data is collected, it's time for the team to study and analyze the results of the changes. This is where you analyze the data collected during the "do" phase and evaluate whether or not your efforts were successful. Managers can present run charts to the PDSA team at regular meetings to understand the progress of their improvement plan. The PDSA team can identify the factors that have contributed to the success of the plan and double down on efforts on similar factors. Analyzing the results also gives insights into the areas that have not generated the desired success. Managers can formulate strategies to improve such areas. Based on the results of your study, you can then make changes to your plan as needed.
Act Phase
Finally, based on the results of their study, the team implements changes (acts) based on their findings. This is where you put your revised plan into action and test it again. Managers can either adopt, adapt, or abandon their quality improvement plan based on their conclusions. By measuring the results of each change and analyzing them, teams can identify areas for improvement and continue to make improvements over time. This process can be repeated until you have achieved the desired results. The PDSA technique can refine the finest processes in an organization and add consistency and effectiveness to them.
What Are the Benefits of Using The PDSA Technique?
The PDSA technique offers a range of benefits for those looking to improve the quality of their products or services. Some of the advantages can be listed as
By following the PDSA cycle, you can ensure that any changes you make are tested and evaluated, allowing you to quickly identify what works and what doesn't. This way, you don't have to waste time and resources on unproductive solutions.
Additionally, the PDSA technique encourages continuous improvement, as the testing and evaluation stages provide valuable feedback for future improvements. You can use this feedback to iterate on your solution, making sure you are always making progress.
Using the PDSA technique also helps to keep everyone involved in the process accountable, as it involves clearly defined roles and responsibilities. Everyone knows what is expected of them and how they fit into the larger picture. This ensures that quality improvements are achieved efficiently and effectively.
Finally, the PDSA technique promotes collaboration between team members and stakeholders as it requires clear communication and dialogue. This allows teams to work together to solve problems and build better solutions. In addition, it encourages an open and transparent culture, as everyone is allowed to express their opinions and ideas.
Conclusion
Getting started with the PDSA technique is straightforward. The idea behind this technique is that it provides a structured approach to testing and evaluating quality improvement efforts. Overall, the PDSA technique provides a simple yet effective way to identify and address problems in any organization. By following the four steps outlined above, you can ensure that your quality improvement efforts are successful and cost-effective.