
Data Structure
Networking
RDBMS
Operating System
Java
MS Excel
iOS
HTML
CSS
Android
Python
C Programming
C++
C#
MongoDB
MySQL
Javascript
PHP
- Selected Reading
- UPSC IAS Exams Notes
- Developer's Best Practices
- Questions and Answers
- Effective Resume Writing
- HR Interview Questions
- Computer Glossary
- Who is Who
Six Sigma Framework: Key Terms Definition
Introduction
The Six Sigma framework is a structured, driven-by-data method for optimizing productivity across the board by decreasing flaws in corporate procedures. The Six Sigma technique was created by Motorola in the 1980s and made famous by General Electric. It is now an increasingly common strategy for attaining organizational excellence in a variety of sectors.
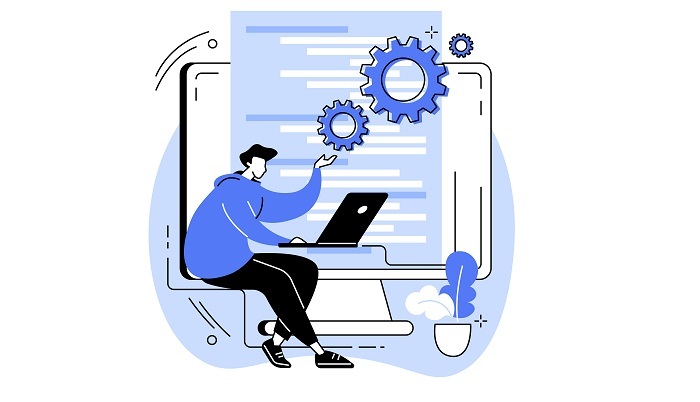
The phrase "Six Sigma" relates to the statistics idea of assessing process variation. The aim of Six Sigma is to reach a state of performance whereby errors or imperfections are exceedingly rare, or about 3.4 mistakes or flaws per million chances (DPMO). Functioning at a "Six Sigma" level, as is regarded as exceptionally effective and produces high-quality outputs, correlates to this degree of productivity. The article gives a brief overview of the Six Sigma framework, emphasizing its main features and advantages.
Six Sigma Phases
Define Phase ? The Six Sigma framework is built upon the Define phase. Organizations identify and describe the issue or improvement opportunity during this phase. Generating goals for the project, defining client needs, and developing a project charter are among the crucial tasks. The effectiveness of the next stages depends on having a well-articulated problem description with concise objectives.
Measure Phase ? collecting information and efficiency evaluation are the main goals of the Measure phase. Organizations monitor important process indicators and pinpoint opportunities for improvement using a variety of data collection approaches.
Analyze Phase ? In the analysis phase, facts are analyzed to determine the underlying reasons for process flaws and inadequacies. Critical elements impacting process efficiency are identified using tools including cause-and-effect diagrams, Pareto charts, and tests of hypotheses
Improve Phase ? During the Improve phase, organizations create and put into action solutions to get rid of or lessen the sources of problem processes. This stage focuses on coming up with original concepts, planning studies, and testing out prospective solutions.
Control Phase ? The Control phase seeks to maintain the advancements made in the previous stages. To guarantee that the method of operation is secure and keeps producing the expected outcomes, organizations set up oversight mechanisms and keep an eye on important process indicators.
Data analysis is useful in determining performance norms, assessing operational variance, and locating constraints. A procedure map or schematic that depicts what is happening and any related metrics is the result of this step.
Organizations may focus on improving and creating customized remedies to deal with the issues found by identifying the reasons behind them.
Organizations may optimize the method, lower faults, and increase effectiveness via thorough testing and data-driven choices. Cross-functional cooperation and the involvement of staff members across all levels are frequently required for the successful carrying out of reforms.
To identify and address any variations from the desired performance, statistical control approaches like control diagrams are used. The goal of the following stage is to save issues from recurring by emphasizing the value of continuing observation, suggestions, and constant improvement.
Benefits of the Six Sigma Framework
Organizations can get a number of advantages from the Six Sigma methodology. Here are several major benefits ?
Improved Quality ? By concentrating on decreasing flaws and faults, Six Sigma assists businesses in producing services and products of higher standards. Greater client happiness, loyalty, and an improved standing in the market result from this
Increased Efficiency and Productivity ? Enhancing procedures, Eliminating Waste, and Optimizing Capacity Utilization: Six Sigma strives for improved Agility and Performance. Organizations may increase efficacy, cut down on cycle times, and boost output by discovering and eliminating non-value-added tasks.
Cost Savings ? Putting Six Sigma into practice may save you a lot of money. Organizations may cut down on revisions, trash, and grievances from clients by minimizing faults and mistakes, which lowers expenses related to waste and subpar quality.
Customer Focus ? Six Sigma places a strong emphasis on comprehending and satisfying client demands. Organizations may offer goods and services that better please their consumers, resulting in a spike in commitment and popularity, by aligning procedures with what they want and require.
Employee Engagement and Skill Development ? Cross-functional teams are used in Six Sigma projects, and employees are encouraged to get involved in initiatives to enhance. In addition to encouraging worker ownership and participation, this offers chances for ability growth and advancement through instruction in quantitative evaluation and resolution techniques.
Results That Are Sustainable ? Six Sigma strives to instill a culture of constant enhancement within organizations. Organizations may maintain the gains made and encourage continued enhancement by institutionalizing the DMAIC method and integrating it into everyday activities.
It's crucial to remember that effective leadership backing, appropriate training, and a dedication to base on information analysis throughout the organization are necessary for adopting Six Sigma properly.
Demerits of the "Six Sigma Framework"
The Six Sigma framework has many advantages, but there are additionally some possible downsides and difficulties when putting it into practice. Here are some important things to remember ?
Time and Resource Consuming ? Six Sigma project implementation necessitates a large amount of time, effort, and expenditure on resources. The technique calls for intensive evaluation of information, education, and process optimization tasks, which can put a burden on the capability of organizations, especially those with smaller sizes.
A Lot of Value Is Placed On Statistical Tools ? Six Sigma makes extensive use of statistical tools and research. Despite the fact that this is helpful for decisions based on data, it occasionally can result in excessive reliance on statistical approaches and complexities, perhaps dominating the actual implementation of solutions or disregarding aesthetic components of development.
Resistance to Change ? Six Sigma implementation frequently necessitates modifications to current procedures, which might be confronted with resistance from personnel and stakeholders who are happy with the current situation system. It might be difficult to get over opposition and promote a change-friendly environment.
Narrow Focus ? The Six Sigma methodology's primary goals are the enhancement of processes and the elimination of defects. Industries such as manufacturing and likely service sectors may benefit from this, but it may not solve more general organizational problems or operational difficulties that call for a different approach or the taking into account other aspects.
Lack of Versatility in Volatile Environments ? Six Sigma is a systematic approach with predetermined stages. This rigidity can be problematic in dynamic or swiftly shifting contexts when adaptability and adaptation are essential to meet new problems or situations.
Limited Application ? According to the business sector or the nature of the issue in question, Six Sigma's efficacy may vary. It works well in organizations with distinct and quantifiable procedures where statistical analysis may be used successfully. Other techniques for problem-solving skills could be more suited to inventive or innovative settings where results can be less certain.
It's crucial to keep in mind that many of these possible negatives may be avoided with thoughtful preparation, stakeholder involvement, and adaptation of the Six Sigma methodology to the unique requirements and circumstances of the organization.
Conclusion
Six Sigma is a structured, data-driven approach used in order to improve the effectiveness of processes, decrease flaws, and eliminate waste. By minimizing mistakes and variances via statistical analysis and methodical figuring out solutions, it seeks to reach an exceptionally high standard of efficiency.
The framework adheres to the DMAIC methodology, which entails setting goals for the project, gauging the effectiveness of processes, examining data, putting changes into practice, and developing systems for oversight.