
Data Structure
Networking
RDBMS
Operating System
Java
MS Excel
iOS
HTML
CSS
Android
Python
C Programming
C++
C#
MongoDB
MySQL
Javascript
PHP
- Selected Reading
- UPSC IAS Exams Notes
- Developer's Best Practices
- Questions and Answers
- Effective Resume Writing
- HR Interview Questions
- Computer Glossary
- Who is Who
Deming vs Juran vs Crosby: Pioneers of Project Management
Introduction
W. Edwards Deming, Joseph M. Juran, and Philip B. Crosby pioneered project management. These three pioneers advanced project quality management. Dr. Deming, an American statistician and management consultant, promoted Total Quality Management (TQM) and project quality. Juran, an engineer and management consultant, introduced the "cost of quality" notion to quality management.
American quality expert Crosby promoted "zero defects" and first-time-right. Continuous improvement, customer focus, and quality planning have shaped project management practices. This article covers their contributions, attitudes, methodologies, and recommended project management tools and practices.
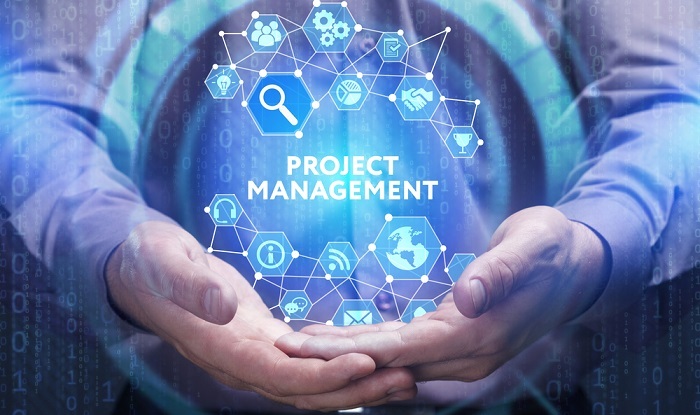
Introduction to Deming, Juran, and Crosby
Overview of Pioneers' Contributions to Project Management
First, Dr. W. Edwards Deming. American statistician and management consultant emphasized project quality. Deming thought that quality should be the first priority in each endeavor because it directly affects customer satisfaction. He established Total Quality Management (TQM), which emphasizes continual improvement, employee interaction, and statistical analysis for high-quality results. Deming's teachings shaped several quality management practices.
Joseph M. Juran, an engineer and management consultant, is up next. Juran is well-known for his work in quality control and management. He emphasized the importance of consumer demands and product/service design. Juran established the "cost of quality," which includes the cost of conformance (preventing faults) and the cost of non-conformance (fixing defects). His ideas convinced organizations to prevent quality issues rather than just cure them.
Finally, we have Philip B. Crosby, an American quality guru. Organizations should aim towards "zero defects," according to Crosby. Instead of inspecting and reworking, he stressed doing things correctly the first time.
Crosby established the "quality improvement process," which has four steps: setting quality requirements, measuring conformance, responding to non-conformance, and constantly improving procedures. Many organizations have adopted proactive quality management principles.
Philosophy and Approach
Fundamental Philosophies and Approaches of Deming, Juran, and Crosby.
Deming's Philosophy and Approach
Deming recommended continuous improvement. He emphasized the significance of understanding the system and its processes. Deming believed quality was the responsibility of everyone.
He emphasized the need for management to play an active role in driving improvement and establishing a quality culture. Deming's PDCA (Plan-Do-Check-Act) cycle gives a methodical approach to problem-solving and improvement.
Juran's Philosophy and Approach
Another significant project management thinker, Joseph M. Juran, focused on the concept of quality planning. Juran said projects should be planned for quality, not examined.
He stressed the importance of defined goals and a systematic approach. Juran's theory centered around the concept of managing quality through a thorough quality planning process, which includes defining quality goals, devising means to attain them, and providing the required resources to support quality initiatives.
Crosby's Philosophy and Approach
Philip B. Crosby advocated for a zero-defect philosophy. He thought preventing problems was better than fixing them. Crosby stressed the necessity of clear expectations, measurable quality standards, and a culture of "doing it right the first time."
He suggested the Four Absolutes of Quality Management, including the idea that quality is compliant with criteria and that prevention is the most cost-effective method.
Focus on Continuous Improvement
Emphasis On Continuous Improvement and Proposed Methods by Deming, Juran, and Crosby
Deming's Approach
Dr. W. Edwards Deming emphasized the significance of taking a systematic approach to continuous improvement. He pushed for the implementation of a quality management concept that includes everyone in an organization.
Deming thought that organizations may achieve long-term success by focusing on long-term progress rather than short-term benefits. The "Plan-Do-Check-Act" (PDCA) cycle he popularised gave a disciplined framework for continuous improvement.
The PDCA Cycle Involves
Plan Identifying areas for improvement, establishing goals, and creating plans.
Do Put the plans into action on a modest scale and collect data.
Check Analysing the data to determine the effectiveness of the modifications done.
Act Based on the results, take necessary actions, such as standardizing successful improvements or revising plans.
Juran's Approach
Another important pioneer in project management, Joseph M. Juran, concentrated on the concept of quality management as a discipline. Juran emphasized the significance of knowing and exceeding customers' expectations. He devised the "Juran Trilogy," a three-step continuous improvement strategy.
The Juran Trilogy Consists of
Quality Planning
Quality planning is the process of identifying customer demands and turning those needs into precise quality goals and standards.
Quality Control
Quality control is the practice of establishing processes and strategies to ensure that products or services satisfy predetermined quality standards.
Quality Improvement
Using problem-solving approaches and data analysis to produce breakthrough improvements in quality.
Crosby's Approach
The concept of "zero defects" as the ultimate goal of quality management was established by Philip B. Crosby. He felt that in order to get optimal results, organizations should strive for error-free performance. Crosby's method of continuous improvement is based on the following principles
Prevention
Preventing flaws is more important than fixing them.
Quality is Free
Investing in quality upfront saves money over dealing with the consequences of poor quality.
Continuous Improvement
Encouraging a culture of continuous improvement throughout the organization.
Customer Orientation and Quality Planning
Emphasis On Customer Orientation and Quality Planning in Project Management
Customer-oriented project planning and execution puts the customer first. It requires knowing and addressing customer needs throughout the project. Project managers prioritize customer satisfaction to produce products and services that meet customer needs.
To achieve customer orientation, project managers must participate in active communication with customers. This clarifies their needs, preferences, and changes to the project. Maintaining an open channel of communication allows project managers to adjust their plans as needed and guarantee that the project meets or exceeds customer expectations.
In the context of project management, quality refers to the degree of perfection or superiority of the final result. Quality must be prioritized throughout the project lifecycle to ensure customer happiness and success. Quality planning helps project managers identify risks and concerns that could affect project quality and address them.
Project managers can improve results by merging customer orientation and quality planning. Projects that focus on client requirements and wants are more likely to offer products and services that resonate with the target audience. Quality planning reduces faults, errors, and rework, improving project efficiency and effectiveness.
Tools and Techniques
Recommended Tools and Techniques for Effective Project Management by Each Pioneer
Deming's Recommended Tools and Techniques
W. Edwards Deming stressed statistical process control and project management improvement. He recommended control charts, Pareto charts, and cause-and-effect diagrams. These tools assist analyze data, identifying trends, and understanding issues. Deming stressed the Plan-Do-Check-Act (PDCA) cycle for problem-solving and decision-making.
Juran's Recommended Tools and Techniques
Joseph M. Juran focused on quality management and believed that quality should be the primary focus of any project. He introduced quality control charts, benchmarking, and the Juran Trilogy?quality planning, control, and improvement. Juran also underlined the necessity of incorporating all personnel in the project and promoting ongoing improvement.
Crosby's Recommended Tools and Techniques
Philip B. Crosby emphasized the concept of zero faults and the importance of prevention above detection. He recommended cost of quality analysis, quality improvement teams, and checklists to assure proper procedure. Crosby also stressed clear communication, setting reasonable goals, and educating personnel to fulfill quality standards.