
Data Structure
Networking
RDBMS
Operating System
Java
MS Excel
iOS
HTML
CSS
Android
Python
C Programming
C++
C#
MongoDB
MySQL
Javascript
PHP
- Selected Reading
- UPSC IAS Exams Notes
- Developer's Best Practices
- Questions and Answers
- Effective Resume Writing
- HR Interview Questions
- Computer Glossary
- Who is Who
5 Most Common Issues with the CAPA Process
Most medical device companies face the corrective and preventive action (CAPA) process year after year.
In order to comply with FDA requirements, companies should have documented the procedures of CAPA and ensure that those procedures are actually followed. CAPA is a common compliance problem companies encounter throughout their design and development cycle despite the regulations being relatively clear.
CAPA Problems: 5 of the Most Common
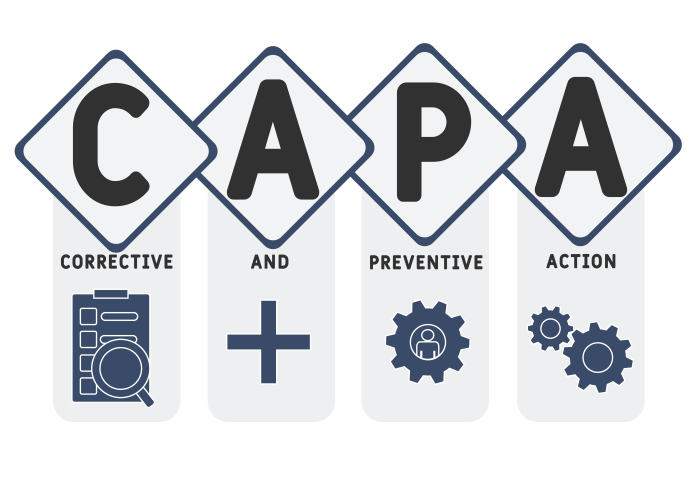
CAPA planning is important for your company's overall success, not just from the regulatory perspective. Let us look at some of the common CAPA problems.
Cross-Functionality is Lacking
Any organization's Quality team typically owns CAPA. Most often, this group decides whether CAPA is needed unilaterally, which makes no sense. As a result, Quality has become the defaulting party for the CAPA issues. In our view, CAPA must be treated as a major project, involving all functions involved in the issue as well.
CAPA can only be accomplished in this way, but many companies do not perform this, leaving quality to deal with it. In an organization, cross-functional teams help provide a holistic and realistic view of what is happening. Putting complete responsibility for a complicated process like CAPA, in the hands of one department will inevitably result in bias and the loss of critical information. A CAPA issue rarely involves only quality.
It is important for a company to balance knowledge across all its departments.
Additionally, management review meetings should be held consistently and cross-functionally. A management review policy must be documented during an inspection. Nowadays, many companies view a management review as an annual or midyear checkbox activity.
Getting pixels from the real picture is all you're doing if you meet a couple of times a year. You may miss or recognize issues when it is too late, as issues can occur at any time. By holding frequent, regular meetings, you'll be able to flag issues more quickly that might justify a CAPA. In the end, the management is responsible for reviewing, assessing, evaluating, preventing, correcting, and controlling quality issues.
A Reactive Approach Rather than a Proactive One
While we've become good at correcting errors, we've become less good at preventing them. Could we set some higher standards? In the event that we strive to eliminate complaints and non-conformances, what might that look like? Proactive design and development begin early - when you think about how to make a product with the least risk.
For example, medical device companies are often forced to make decisions based on lagging data, which poses a challenge. It is difficult to collect leading data when a complaint is related to certain things that have already occurred. A proactive approach might include asking customers for feedback or conducting surveys before any issues arise.
In order to mitigate risk, many companies add disclaimers to their product labels. For the device to meet all user needs and be developed according to its intended purpose, there can be a more proactive approach taken. CAPAs should be managed in the same way.
It is not possible for you to expect that the criteria that have been published will be applicable to every company and device. According to their own product knowledge, companies should create their criteria (including regulatory requirements). To prevent symptoms from occurring in the first place, we have to implement the required steps before any symptoms arise.
Overuse vs. Underuse
Do CAPAs get used too often or not often enough?
There are many processes that contribute to the CAPA process. You should be diligent and scrutinize what needs CAPAs and what doesn't. A CAPA is not required for every problem you encounter!
Can you tell when you should publish a CAPA, and when you shouldn't? The purpose of a CAPA is to solve a systemic problem. CAPAs will overburden the capital and resources, and lead to costly mistakes if you turn every complaint into one.
The same goes for waiting until something goes wrong before you produce a CAPA. Investigate whether any other products or processes use that fitting if a fitting is not working as it should. Using a CAPA, you can solve any issues much sooner than if they were not addressed.
Determination of the Root Cause is Poor
It often seems that little time is spent identifying the root cause of a problem. When attempting to determine the root cause, it is common to simply put the issue with different words. It is not the root cause of the problem - it is just a symptom.
In the event that the root cause isn't properly identified and defined, you're likely to face the same problem again, possibly as a recurring issue, and this is because the actual root cause was never resolved.
A number of different methods can be used to identify the root cause of a problem. You can always opt for the "5 Whys" technique to identify the root cause of the problem. Essentially, it includes asking five "why" queries until you determine a root cause and can take action on it. It depends on the particular situation, and sometimes it only takes a couple of questions, while other times it takes closer to ten.
The CAPA Process is Poorly Defined
Above 483 observations have been issued during inspections due to CAPAs over the last few years. If you have received an observation, it means any of the following ?
There is a lack of compliance with your defined CAPA procedure.
The CAPA process you have defined is not compliant.
A CAPA procedure has not been defined.
A similar theme appears to be emerging. So, what has to be done to avoid getting into this situation? As we mentioned previously in the article, let's be proactive. Ensure your CAPA process is properly working by conducting an annual internal review to determine if anything needs to be changed. You can also learn to be proactive by taking a holistic approach to managing CAPAs. To minimize or eliminate the need for corrective action, we should be proactive first.
Conclusion
Your quality system must always include CAPA management. Fortunately, if an organization manages its problems properly, the expense and exhaustive problems can be avoided. You should look into your CAPA procedures and implement all the required changes to avoid corrections.