
Data Structure
Networking
RDBMS
Operating System
Java
MS Excel
iOS
HTML
CSS
Android
Python
C Programming
C++
C#
MongoDB
MySQL
Javascript
PHP
- Selected Reading
- UPSC IAS Exams Notes
- Developer's Best Practices
- Questions and Answers
- Effective Resume Writing
- HR Interview Questions
- Computer Glossary
- Who is Who
Brushless DC Motors
An electric motor is an energy conversion device that converts electrical energy into mechanical energy. Therefore, the input to an electric motor is electricity, while the output of the electric motor is mechanical energy in the form of rotation of the shaft.
Based on the type of electrical energy that motor requires to operate, the electric motors are classified into two types, i.e. AC Motor and DC Motor.
An AC Motor or alternating current motor is one that transforms electrical energy in the form of alternating current into rotational mechanical energy. On the other hand, an electric motor which transforms direct current electrical energy into rotational mechanical energy is called a DC motor or direct current motor.
AC and DC motors are further classified into the following types ?
AC Motors ?
Induction Motor (also called asynchronous motor)
Synchronous Motor
DC Motors ?
Brushed DC Motor
Brushless DC Motor
This article is meant for explaining the Brushless DC Motors (BLDC Motors), their working, types, advantages, disadvantages, and applications. So, let us start discussing about the brushless DC motors.
What is a Brushless DC Motor?
The type of direct current motor which does not have carbon brushes for commutation is referred to as a brushless DC motor. Brushless DC motor is also known as BLDC motor or BL Motor.
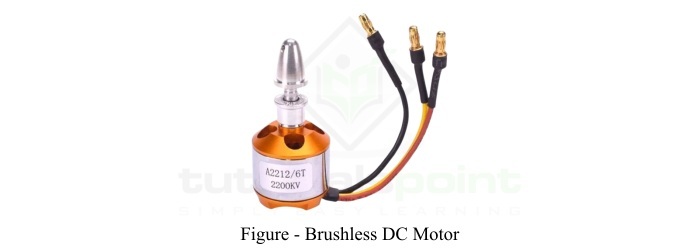
A brushless DC motor is a type of electronically commuted DC motor. Hence, sometimes, the brushless DC motors are also referred to as EC motors. The important characteristics of a BLDC motor is its high efficiency. This is because, the rotor of the brushless DC motor forms the magnetic field system by permanent magnets and hence, it does not require any electric power. Therefore, there is no need of commutator and brushes to make connections with rotating parts.
In place of commutator and brushes, the brushless DC motors consist of an electronic control circuit to determine the rotor position.
Construction of Brushless DC Motor
Similar to any other electric motor, the brushless DC motor also consists of two major parts,i.e. stator and rotor.
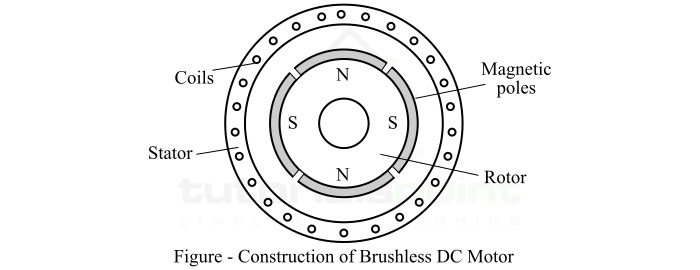
In the case of brushless DC motors, the stator consists of the armature winding, while the rotor consists of the permanent magnets. These motors use electronic commutation system to convert electrical energy into mechanical energy. Therefore, in brushless DC motors, the mechanical commutator in brushed DC motor is replaced with an electronic switching circuit.
In the brushless DC motors, the magnetic field is switched with the help of an amplifier that is triggered by a commutating device such as an encoder.
Therefore, the brushless DC motor consists of a rotor with permanent magnets and a stator with armature windings. The stator armature windings are energized from a DC supply in a sequence to produce a rotating magnetic field which interacts with the rotor magnets and causes it to rotate.
In a BLDC motor, the electronic controller uses an encoder or a Hall Effect sensor to detect the position of the rotor and regulates the current through the armature winding accordingly. This allows the brushless DC motor to operate smoothly and efficiently.
The other major components of the brushless DC motor include rotor shaft, bearings, cooling system, etc. Hence, the overall construction of a brushless DC motor is more complex as compared to an ordinary brushed DC motor.
Types of Brushless DC Motors
The classification of brushless DC motors based on different parameters is done as follows ?
Types of Brushless DC Motors Based on Design
In-runner Brushless DC Motor
Out-runner Brushless DC Motor
Types of Brushless DC Motors Based on Sensor
Sensored Brushless DC Motor
Sensorless Brushless DC Motor
Types of Brushless DC Motors Based on Number of Poles
Single-Pole Brushless DC Motor
Multi-Pole Brushless DC Motor
Types of Brushless DC Motors Based on the Type of Power Single
Trapezoidal Brushless DC Motor
Sinusoidal Brushless DC Motor
Now, let us briefly discuss each type of brushless DC motor.
In-Runner Brushless DC Motor
This type of BLDC motor consists of a rotor with permanent magnets inside the stator. In the in-runner brushless motor, the stator windings are mounted on the casing of the motor. This type of brushless DC motor is best suited for applications that require high speed.
Out-Runner Brushless DC Motor
The out-runner brushless DC motor consists of a rotor with permanent magnet outside the stator. Hence, this BLDC motor uses a rotating outer case that can rotate around a stationary inner-piece. This type of brushless DC motor is suitable for low speed and high torque applications.
Sensored Brushless DC Motor
The type of brushless DC motor which uses sensors to collect data related to the rotor position is known as a sensored brushless DC motor. These motor works efficiently at low speeds, but they cannot operate reliably in harsh conditions like dusty and high temperature environment. Hence, the sensored brushless DC motors are best suited for low speed applications.
Sensorless Brushless DC Motor
This type of brushless DC motors does not use sensors to provide rotor position data, instead they collect rotor position data from back electromotive forces generated in the stator windings. This type of brushless DC motors are suitable for high-speed applications. Also, these can be used in harsh conditions.
Single-Pole Brushless DC Motor
In this type of BLDC motor, the rotor consists of only one pair of magnetic poles, i.e. one north pole and one south pole. The single pole BLDC motor can run at very high speeds. But, at low speeds, the performance of the motor degrades significantly. Hence, this type of BLDC motor is also best suited for high speed applications.
Multi-Pole Brushless DC Motor
This type of brushless DC motor has multiple pole pairs on the rotor. The increased number of rotor poles provide a smoother operation but at lower speeds. Therefore, this type of brushless DC motor is suitable for high-torque and low-speed applications.
Trapezoidal Brushless DC Motor
This type of brushless DC motor uses a power signal having a trapezoidal shaped waveform. The major advantage of this motor is that it has a simple commutation method. However, at low speeds, the trapezoidal signal causes the torque ripple effect which makes the operation of the motor less smooth. But, at high speeds, this type of brushless motor performs better, hence is suitable for high-speed applications.
Sinusoidal Brushless DC Motor
This type of brushless DC motor is power by a signal that have sinusoidal waveform. The sinusoidal brushless DC motor runs smoothly at low speeds, but the torque of this motor is reduced at higher speeds. Hence, this type of motor is best suited for low-speed applications.
Advantages of Brushless DC Motors
The main advantages of brushless DC (BLDC) motors are as follows ?
Brushless DC motors are more efficient than brushed DC motors due to absence of carbon brushes and mechanical commutator.
Brushless DC motors has less energy losses.
Brushless DC motors has a wear and tear, and hence, longer life span.
The maintenance cost of brushless DC motors is low as there is no need of brush replacement.
Brushless DC motors have noise and vibration free operation.
In terms of torque, speed control, power output, etc. the brushless DC motors offer better performance.
Brushless DC motors have less electromagnetic interference.
Brushless DC motors have high dynamic response.
Disadvantages of Brushless DC Motors
The major disadvantages of brushless DC motors are listed below ?
The initial cost of brushless DC motors is more than that of brushed DC motors.
It requires expensive electronic controllers for commutation of the motor.
Brushless DC motors are more sensitive to overheating.
They require efficient and expensive cooling system to ensure reliable operation.
Applications of Brushless DC Motors
Brushless DC motors are used in several applications. Some of them are listed below ?
Brushless DC motors are used in electric vehicles.
Brushless DC motors are used in drones, robots, and many other robotic equipment.
Brushless DC motors are also used in several medical instruments like infusion pumps, ventilators, etc.
Brushless DC motors are also used in fans and air conditioners due to their quiet and efficient operation.
Brushless DC motors are also used in several electronic devices such as hard disk drives, CD/DVD players, CPU fans, etc.
Conclusion
In conclusion, a brushless DC motor is an efficient type of DC motor that is widely being used in several modern electronic devices. However, the construction of brushless motors is more complex which makes them relatively expensive as compared to brushed DC motors. But these motors require less maintenance, which reduces the operation cost. The advantages of BLDC motors over brushed DC motors make them to use in a range of applications.